اگر به فکر راه اندازی یک کسب و کار هستید، یکی از صنایعی که امروزه مورد توجه قرار گرفته تولید پودر شستشوی لباس یا پودر شوینده است. بعلاوه، هرکسی می تواند کسب و کار تولید شوینده را راه اندازی کند. شما برای راه اندازی این کسب و کار نیاز به سرمایه اولیه خیلی زیاد ندارید.آیا به دنبال راه اندازی کسب و کار تولید پودر شوینده هستید؟ اگر پاسختان مثبت است، این مقاله مخصوص شماست! با ما همراه باشید.
درباره پودرهای شوینده
پودرهای شوینده و شستشو سورفکتانت ها هستند. این ها، ضروری ترین اجزای سازنده با اهداف پاک کنندگی و شستشو هستند. به طور کلی، امروزه دو نوع فناوری تولید پودر شوینده وجود دارد. در یکی از این فناوری ها مواد خام با یکدیگر مخلوط می شوند و در دیگری از روش خشک کننده اسپری یا spray dryer استفاده می شود. به هر حال، باید در ذهن داشته باشید که اولین گزینه برای تولید انبوه و صنعتی پودر شوینده انتخاب مناسبی برای شماست. اولین انتخاب ممکن است نیاز به سرمایه اولیه بیشتر داشته باشد. دومین گزینه آسان تر است. در این جا، می توانید با هزینه کمتر فرایند تولید را شروع کنید.
کسب و کار تولید شوینده
پتانسیل بازار
در سال های اخیر، به خاطر رشد جمعیت و نیاز مردم امروزی به شوینده ها تقاضا برای پودرهای شوینده نیز افزایش یافته است. به علت گسترش شهر نشینی، تقاضا برای پودرهای شوینده هم به صورت فله ای و هم در بسته بندی های با سایز کوچک افزایش یافته است. علاوه بر این، به علت افزایش درآمد خانوارها، ظرفیت خرید جامعه برای تهیه شوینده ها افزایش یافته است. بنابراین، تولید پودر شوینده فرصتی کاملا سودآوری است برای کسانی که قصد راه اندازی کسب و کار دارند.
نصب ماشین آلات و دستگاه ها
برای راه اندازی کارگاه تولید پودر شوینده به 300 متر مربع فضا نیاز دارید. البته فضای نهایی بستگی به میزان تولید شما دارد. شما نیاز به محلی امن دارید که حمل و نقل به آنجا آسان باشد و امکانات آب و برق نیز برای آن فراهم باشد.
ماشین آلات
برخی از تجهیزاتی که برای تولید پودر شوینده نیاز دارید در زیر معرفی شده اند:
- راکتورها (Reactors)
- پودرساز (Pulveriser)
- ترازو (Weighing Scale)
- مخلوط کن (Blender)
- خنثی کننده (Neutraliser)
- توری ریز (fine screen)
- جداکننده (Separator)
- میکسر (mixer)
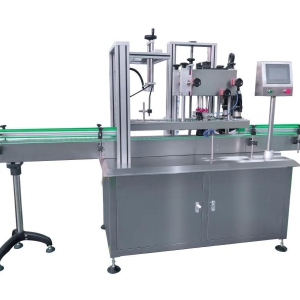
فرمول های ساخت پودر شوینده
هر کمپانی فرمولاسیون مخصوص به خود را جهت ساخت پودر شوینده استفاده می کند. بسته به بازار هدف، شما باید فرمول منحصر به فرد خود را داشته باشید. شما می توانید فناوری ساخت مورد نیاز را از محققان و دانشگاه ها یا مراکز معتبر تهیه کنید.
برای کمک به شما، فرمول پایه و درصد اجزای سازنده برای ساخت پودر شوینده را در زیر ارایه نموده ایم:
اجرای سازنده و درصد وزنی:
- LAB acid slurry فعال 85 درصد/ 18 درصد وزنی
- سدیم کربنات (خاکستر سودا)/35 درصد وزنی
- سدیم متاسیلیکات/ 2 درصد وزنی
- سدیم بیکربنات/10 درصد وزنی
- سدیم تری پلی فسفات/10 درصد وزنی
- سدیم کربوکسی متیل سلولز/1.5 درصد وزنی
- رنگ آبی فتالوسیانین یا رنگ زرد محلول در روغن/0.1 درصد وزنی
- عطر 0.1
- سفید کننده نوری/0.3 درصد وزنی
- آب/ 3 درصد وزنی
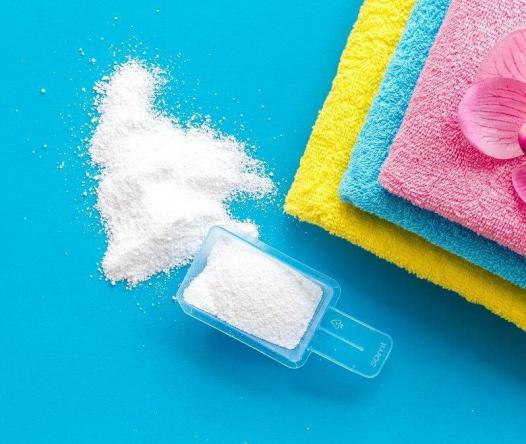
فرایند تولید
در اینجا نحوه تولید پودر شوینده را توضیح می دهیم:
- با استفاده از خاکستر سودا، acid slurry را خنثی می کنیم.
- سپس، برای آنکه واکنش تکمیل شود مخلوط کردن مواد را به مدت 1 ساعت ادامه می دهیم.
- تمامی مواد افزودنی نظیر رنگ ها، نمک، عطر، تری سیدم فسفات و … را اضافه می کنیم.
- پس از مخلوط کردن افزودنی ها، به هم زدن مخلوط ادامه می دهیم تا مخلوط کاملا یکدست و همگن شود.
- سپس مخلوط را خشک می کنیم.
- سرانجام محصول نهایی را بسته بندی می کنیم. مطمئن شوید از که از بسته بندی مناسب برای این کار استفاده می کنید.
بسته بندی پودر شوینده
در کنار مواد خام معرفی شده در بالا، شما باید به دنبال بسته بندی مناسب برای پورد شوینده خود باشید. به طور کلی، پودر شوینده به صورت فله ای یا بسته بندی های 250 گرم، 500 گرم، 1 کیلو گرم یا 5 کیلو گرم عرضه می شود. در مورد بسته بندی خوب فکر کنید چون تاثیر بسزایی در جذب مشتری دارد. شما باید بسته بندی را بر اساس سلیقه مشتری طراحی کنید. بر روی بسته بندی اطلاعات کامل در مورد تاریخ تولید، تاریخ انقضا، کمیت، اجزای سازنده و … را درج کنید. در صورت امکان از مواد اولیه سازگار با محیط زیست استفاده کنید. در گرمایش زمین سهیم نباشید!
فرآیند مخلوط کن (میکسر)
ابتدا، مواد در یکی از دو دستگاه قرار میگیرند: مخلوط کن غلتکی یا مخلوط کن نواری. مخلوط کن غلتکی که به شکل جعبه مستطیلی شکل است، توسط دستگاهی از بیرون چرخانده و تکان داده می شود، در حالی که مخلوط کن نواری استوانه ای است که دارای تیغه هایی برای خراشیدن و مخلوط کردن مواد است. پس از مخلوط شدن مواد داخل مخلوط کن، دری در ته خمره یا همان میکسر باز می شود. در حالی که مخلوط کن هنوز مواد را به هم می زند، به مخلوط اجازه داده می شود تا روی یک تسمه نقاله یا دستگاه کانالی دیگر خالی شود. سپس تسمه پودر لباسشویی را به محل دیگری از کارخانه منتقل میکند و میتوان آن را در جعبهها یا کارتنها بسته بندی تا به عمدهفروشان یا توزیعکننده تحویل شود.
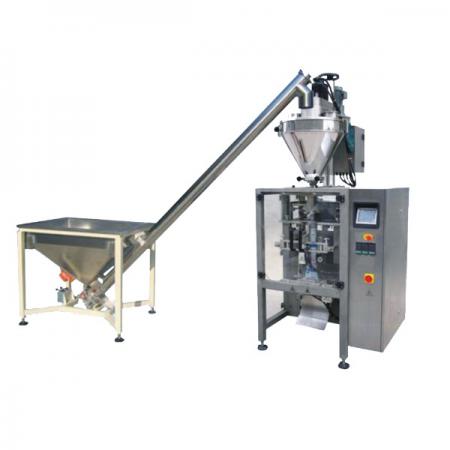
فرآیند تراکم یا انباشتگی
در این روش، مواد خشک برای یک شوینده ابتدا به یک دستگاه بزرگ معروف به آگلومراتور Shuggi (سازنده Shuggi) وارد می شود. در داخل آگلومراتور، تیغه های تیز و چرخان، مواد را با غلظت خوبی مخلوط می کنند. این فرآیند شبیه بافت مواد غذایی است که در داخل یک غذاساز تولید میشوند. پس از مخلوط شدن مواد خشک، مواد مایع از طریق نازل های نصب شده در دیواره های آگلومراتور روی مخلوط خشک اسپری می شوند. اختلاط ادامه می یابد و باعث ایجاد یک واکنش گرمازا (تولید گرما) می شود. مخلوط حاصل، مایعی داغ و چسبناک شبیه ژلاتین است که سفت نشده است. در مرحله بعد، به مایع اجازه داده می شود تا از آگلومراتور خارج شود. هنگامی که از دستگاه خارج می شود، روی یک تسمه خشککن جمع میشود، نواری که گرمای خود را دارد، قرار گرفتن در معرض هوا و دمندههای هوای داغ آن را شکننده میکند – و خرد کردن یا خرد شدن آن را آسان می کند. سپس مواد شوینده پودر می شود و از طریق صفحه های اندازه گیری فشار داده می شود که اطمینان حاصل می کند که هیچ توده بزرگی از محصول مخلوط نشده به بازار نمی رود. نتیجه این فرآیند یک ماده شوینده خشک است که از دانه های ماده شوینده مخلوط تشکیل شده است.
روش دوغاب یا همان آبکی
در این فرآیند، مواد در آب حل می شوند تا دوغاب ایجاد شود. با یک پمپ، دوغاب از طریق نازل های داخل بالای یک ظرف مخروطی شکل پاشیده می شود، زیرا هوای گرم و خشک به طور همزمان به پایین مخروط وارد می شود. همانطور که دوغاب خشک می شود، “دانه های” مواد شوینده خشک به پایین مخروط می افتند، جایی که می توان آنها را برای بسته بندی جمع آوری کرد
مایع پاک کننده
اگر قرار است ماده شوینده به جای پودر، مایع باشد، پس از مخلوط شدن همه مواد با محلولی متشکل از آب و مواد شیمیایی مختلف که به عنوان حل کننده شناخته می شوند، دوباره در آن مخلوط می شود. حل کننده ها به آب و مواد شوینده کمک می کنند تا بطور کامل و یکنواخت با هم ترکیب شوند.
کنترل کیفیت پودر لباسشویی
تولیدکنندگان به طور مداوم بر کیفیت مواد شوینده خود نظارت می کنند و از همان روش های آزمایشگاهی برای ارزیابی اثربخشی محصولات جدید استفاده می کنند. در یک روش، نور به پارچه ای که کثیف شده است تابیده می شود و سپس با ماده شوینده نمونه شسته می شود. مقدار نور بازتاب شده در مقایسه با مقدار بازتاب شده توسط نمونه پارچه اصلی، معیاری برای تمیزی است. نرخ انعکاس 98 درصد کاملاً خوب در نظر گرفته می شود و نشان می دهد که مواد شوینده به درستی کار خود را انجام داده است. روش دیگر شامل سوزاندن آزمایشگاهی مقدار کمی از مواد است که کثیف شده و سپس شسته شده است. وزن خاکستر، به اضافه وزن نتایج گازی حاصل از سوزاندن، نشان می دهد که چه مقدار از کثیفی پس از شستشو در پارچه باقی مانده است. نتیجه ای که بسیار بالاتر از نمونه آزمایشی بالا است نشان می دهد که مقدار قابل توجهی کثیفی در نمونه شسته شده باقی مانده است. به طور طبیعی، هدف این است که تا حد امکان به وزن یک نمونه کنترل تمیز نزدیک شود.
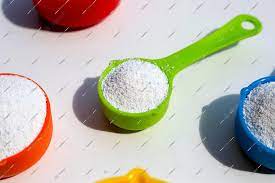
محصولات جانبی
در سال های اخیر، صنایع شوینده های پودر لباسشویی با دو چالش زیست محیطی مواجه بوده اند که به نظر می رسد با هر دوی آنها با موفقیت مقابله شده است. محیط بانان نگران بودند که سازندگان فسفات مقادیر زیادی ترکیبات فسفری را به آبراهه های کشور وارد می کنند. فسفر که به عنوان کود عمل می کند، رشد جلبک ها را تحریک می کند و این محصولات غیرطبیعی بزرگ جلبک ها به طور قابل توجهی میزان اکسیژن محلول در آب را کاهش می دهند. این کاهش در اکسیژن آزاد به دیگر جانداران دریایی آسیب رساند، بنابراین الگوهای طبیعی اکولوژیکی را تهدید می کند. این مشکل و فشار زیست محیطی و قوانینی که در اواخر دهه 1960 ایجاد کرد، تولیدکنندگان را به ساخت مواد اولیه شیمیایی مؤثرتری سوق داد که حاوی فسفات نیستند. امروزه مواد شوینده ای که در بسیاری از ایالت ها فروخته می شوند، فاقد فسفات هستند. اگرچه این تعدیل مستلزم تغییری در فرآیند تولید نبود، اما به تلاشی تحقیقاتی نیاز داشت که چندین ماه طول کشید تا یک جایگزین رضایت بخش ابداع شود. یکی از مشکلات زیست محیطی قبلی، فوم مواد شوینده اضافی بود که در آبراهه های کشور ظاهر می شد. در اوایل دهه 1950، زمانی که استفاده خانگی از ماشینهای لباسشویی و پودرلباسشویی و دیگر شوینده های لباسشویی با سرعت انفجاری رشد کرد، موارد متعددی از ظاهر شدن مقادیر زیادی کف در رودخانهها و جویها مشاهده شد، اگرچه مواد شوینده ممکن است تنها عامل ایجاد کف نبوده باشد. در طی یک دوره پنج ساله، از سال 1951 تا 1956، مشخص شد که یک سورفاکتانت معمولی، ABS (آلکیل بنزن سولفونات)، ماده شوینده ای که به کف کردن کمک می کند، مسئول است. ساختار مولکولی پیچیده ABS آنقدر سریع تجزیه نمی شود که پس از تخلیه آب شستشو از کف نکند. جایگزین اثبات شده بلافاصله در دسترس نبود. با این حال، از آغاز سال 1956، سازندگان ABS را با LAS (آلکیلات سولفونات خطی) جایگزین کردند که به سرعت تجزیه می شود و از آن زمان، LAS عامل کف کننده اولیه در مواد شوینده بوده است.
مواد پاک کننده لباسشویی یا پودر لباسشویی نوعی مواد شوینده (تمیز کننده) است که برای تمیز کردن لباس استفاده میشود. مواد شوینده لباسشویی به صورت پودر و مایع تولید میشود.در حالی که مواد شوینده پودری و مایع سهم تقریباً مساوی از بازار شویندههای لباسشویی در سراسر جهان را از نظر ارزش دارند ، مواد شوینده پودری از نظر حجم دو برابر بیشتر از مایعات به فروش میرسند.پودرهای شستشو رایجترین مواد شوینده برای شستن لباسهای ما هستند.و سال هاست که هیچ جایگزینی برای آنها وجود ندارد اما جادوی آنها چیست؟ آنها ضمن محافظت از لباسهای رنگی از محو شدن ، با سختترین لکهها میجنگند . آنها به طور موثری آب را نرم میکنند ، و بیشتر باعث افزایش اثربخشی تمیز کردن و از جمله دیگر کاهش ضربات پارچه میشوند. تقریباً همیشه میتوان نتایج خوبی از شستن هنگام استفاده از پودرهای شستشو انتظار داشت. امروزه پودرهای شستشو بر اساس آخرین فناوریها فرمولهای برتر وجود دارند. با انتخابهای بسیاری در بازار ، حتماً یک پاک کننده لباسشویی پیدا کرده اید که متناسب با بودجه شما باشد و نیازهای شما را برای تمیز کردن لباسهای شسته شده و همچنین اولویت خانواده شما از عطر و مسئولیت زیست محیطی برآورده کند. مواد شوینده مخصوص به صورت مایع ، پودر در دسترس هستند. همه اشکال مواد شوینده لباسشویی لباسها را به خوبی تمیز میکند.مواد شوینده پودری معمولاً برای استفاده در هر بار ارزانتر هستند. آنها درپاک کردن لکههای گل و خاک در لباس مؤثر هستند.در صورت داشتن آب بسیار سرد برای شستشو استفاده از مواد شوینده پودری میتواند مشکل ساز باشد زیرا ممکن است کاملاً حل نشوند. قبل از افزودن لباس و آب ، همیشه مواد شوینده پودری را به درام واشر اضافه کنید. در صورت بروز مشکلات باقیمانده ، مواد شوینده را با یک چهارم آب گرم مخلوط کرده و قبل از انجام بار شستشو ، مستقیماً آن را درام واشر اضافه کنید.
پودرلباسشویی مناسب شستشوی لباس
سالهای زیادی است که در ایران شرکتهای مختلف شوینده در حال رقابت با یکدیگر هستند و برندهای مختلفی نیز وجود دارد.اما پودر مناسب لباسشویی چه نوع پودری است؟پودرها با توجه به ویژگی و استاندارد به پودرلباسشویی لباسهای رنگی،لباسهای کودک و لباسهای سفید و…تقسیم میشوند.این پودرها که با توجه به کاربردشان ومتناسب با پارچه و جنس و رنگ تولید میشوند به لباس آسیب نمیرسانند و باعث از بین بردن لکههای لباس میشوند.بدون اینکه صدمه ای به پارچه وارد شود. برای مثال پودر شستشوی لباسهای سفید از پاک کنندگی قویتری برخوردار هستند و درخشندگی بیشتری به لباس میدهند اما اگر برای این پارچه از پودر شستشوی نامناسبی استفاده شود باعث صدمه به لباس و پاک نشدن لکه میگردد.
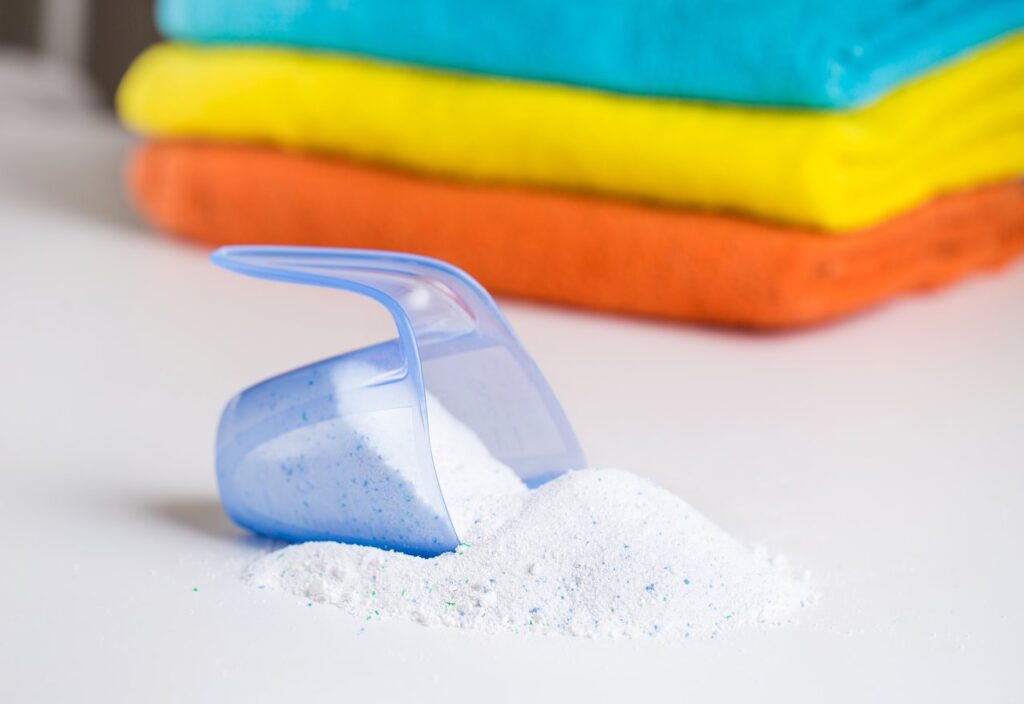
مواد اولیه پودر لباسشویی
سورفاکتانتها
مولكولهایی شامل دو قسمت هیدروفوب (آبگریز، نامحلول در آب) و هیدروفیل (آبدوست، محلول در آب ) هستند.این مولكولها دارای فعالیت بسیار بالایی در حد واسط بین هوا و آب یا روغن و آب میباشند.این مواد دارای نامهای متعددی از قبیل مواد فعال سطحی،دترجنتها و یا بطور ساده اكتیو میباشند.سورفاكتانتها كشش سطحی آب را كاهش داده و منجر به افزایش مرطوب شدن سطوح میشوند. سورفاكتانتها شل شدن و جداسازی چرك در طی شستشو و همچنین معلق سازی چرك را در محلول شستشو بر عهده دارند. چهار دسته عمده سورفاكتانتها عبارتند از :
وقتی كه گروه قطبی كه از طریق پیوند كووالانسی به قسمت هیدروفوب سورفاكتانت متصل است دارای بار منفی باشد(R-CO2- ,R-SO4- ,R-SO3-)، سورفاكتانت آنیونیك نامیده می شود. مانند صابونها، آلكیل بنزن سولفونات هاو فتی الكل سولفاتها .
وقتی كه گروه قطبی كه از طریق پیوند كووالانسی به قسمت هیدروفوب سورفاكتانت متصل است دارای بار مثبت باشد (N+R1R2R3R4)، سورفاكتانت كاتیونیك نامیده می شود. مانند دی متیل دی استئاریل آمونیوم كلراید. سورفاكتانتهای كاتیونیك اغلب به عنوان نرم كننده پارچه و عوامل آنتی استاتیك كاربرد دارند.
سورفاكتانتهای نانیونیك دارای گروه قطبی می باشند كه نمی تواند در محلول آبی یونیزه شود. قسمت هیدروفوب شامل زنجیر چرب و قسمت هیدروفیل شامل اتمهای غیر قابل یونیزه اكسیژن، نیتروژن یا سولفور است.حلالیت نتیجه تشكیل پیوند هیدروژنی بین آب و گروههای هیدروفیل مانند گروههای اتری پلی اكسی اتیلن میباشد. در این طبقه بندی بسیاری از مشتقات پلی اكسی اتیلن یا پلی اكسی پروپیلن و آلكانول آمیدها و آلكیل آمینهای اتوكسیله قرار می گیرد.
مولكولهایی هستند كه تشكیل یون دوقطبی می دهند.درpH پائین شبیه كاتیونیكها ودر pH بالا شبیه آنیونیكها عمل میكنند. در pH متوسط دارای دو بار مثبت و منفی هستند، یعنی ساختار یون دو قطبی پیدا می كنند. در این طبقه كوكو آمیدو پروپیل بتائین بیشترین كاربرد را داراست.
آنزیم ها:
آنزیمها مولكولهای پروتئینی می باشند كه بدلیل داشتن ماهیت كاتالیكی می توانند بسیاری از لكه های پروتئینی و چربی ونشاسته ای را كه در مقابل دترجنتها مقاومند تجزیه نمایند. آنزیمهای مورد مصرف در صنایع شوینده عبارتند از:
- آنزیم پروتئاز: تجزیه لكه های پروتئینی مانندلكه های غذایی شیر، تخم مرغ، گیاهان، خون
- آنزیم لیپاز: تجزیه لكه های چربی
- آنزیم آمیلاز: تجزیه لكه های نشاسته ای مانند مواد قندی
- آنزیم سلولاز: تشكیل میكروفیبریلها (پرزها) روی سطوح پارچه ها در طی عمكرد مكانیكی ماشین، منجر به پخش نور شده وسطح پارچه در نظر بیننده ، ظاهری خاكستری پیدا می كند.این بدین معنی است كه رنگ پارچه ظاهر تیره ای به خود می گیرد.آنزیم سلولاز با حذف این پرزها از سطوح، وضوح اولیه رنگ را برمی گرداند. علاوه بر این ، آنزیم سلولاز قابلیت حذف لكه های خیلی عمیق موجود در الیاف را دارا می باشد.
برای پایداری آنزیم ها در مایعات بویژه آنزیم پروتئاز،کارخانه های تولیدکننده معمولا از نمكهای بوریك اسید ،دی یا تری ال هاوآلكانول آمینها در فرمولاسیون شوینده های لباس استفاده می كنند.
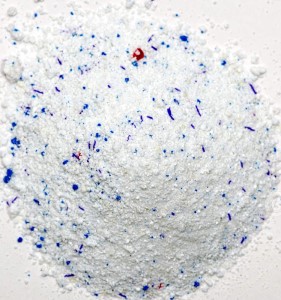
ماشین آلات و تجهیزات لازم برای تولید
مخزن ۲ جداره همزن دار ۲۰۰ لیتری از استنلس استیل ( ۱۲۰ کیلوگرم)
مخزن ۱ جداره همزن دار ۲۰۰ لیتری از استنلس استیل (۶۰ کیلوگرم)
بلندر ۲ جداره ۲۲۰۰ لیتری مدل MH 2000
پمپ دنده ای دو اینچ از استنلس استیل با موتور گیربکس ۳HP
کوره خشک کن است استنلس استیل ROT 3
هواساز ۳۲۵ متر مکعب بر دقیقه با قدرت حرارتی ۲۲۰۰۰۰
سرد کن از نوع دوار
فن ۳۰ متر مکعب بر دقیقه
گرانولاتور از استنلس تیپ HAM
بلندر مدل MH2000 و ۲۲۰۰ لیتری همراه با سیستم پاشش
سیستم پاشش با پمپ سانتریفیوژ با قیف ۲۰۰ لیتر از استنلس استیل
سرند ویبره از فولاد کربی با خروجی یک تن
پرکن پودر برای بسته بندی یک کیلویی در قوطی تیپ CUPA
پرکن پودر برای بسته بندی ۱ الی ۵۰ کیلو به صورت دیجیتالی
کانوایر تسمه ای با طول چهار متر عاج دار
پرس پنوماتیک
تفاوت شوینده ماشین لباسشویی و دستی
همانطور که در بالا هم ذکر کردیم، شویندهها در انوع مختلف پودری، مایع، آنزیمدار، بدون آنزیم، دستی، ماشینی و … عرضه میشوند. هریک از شویندهها، ویژگی مخصوص و کاربرد متفاوتی دارند که باعث تفاوت شوینده ماشین لباسشویی و دستی میشود. به همین خاطر، نمیتوان گفت که کدام یک از آنها بهتر است. شویندهها دستی نیاز به 10 تا 15 دقیقه زمان برای حلشدن در آب دارند. در صورتی که شویندههای ماشین لباسشویی، با سرعت در آب حل میشوند. به همین خاطر، اگر از پودرهای دستی در ماشین استفاده شود، قبل از آنکه شوینده به طور کامل در آب حل شود، زمان شستشو به پایان میرسد و باعث ایجاد اختلال در فرآیند شستشو و کثیف ماندن لباسها میشود. میزان کفکنندگی را میتوان اصلیترین تفاوت شوینده ماشین لباسشویی و دستی دانست؛ زیرا، این کفها به مرور باعث خرابی سیستمهای الکتریکی دستگاه میشود. پودر شوینده ماشین لباسشویی با تولید کف کنترل شده، مانع از خرابی دستگاه یا خوردگی اجزاء آن میشود. فرمولاسیون شویندههای دستی به گونهای طراحی شده است که دارای سازگاری با پوست باشد و مانع از بروز بیماری و آلرژیهای پوستی شود. در صورتی که هنگام کار با شوینده ماشین لباسشویی، ترکیبات شیمیایی شوینده ماشین میتوانند باعث بروز سوزش، خارش و حساسیتهای پوستی شوند. اگر کف حاصل از مواد شوینده ماشین لباسشویی به درون چشم یا صورت بپاشد، باعث آسیب دیدن چشمها میشود. از دیگر تفاوت شوینده ماشین لباسشویی و دستی، وجود بلیچ در شویندههای ماشینی است. این آنزیمها دارای قدرت پاککنندگی بالا هستند و باعث از بین رفتن لکه از روی پارچه میشوند؛ همچنین، مانع از نشست مجدد باکتری و چرک بر روی پارچه میشود. برای از بین بردن لکههای قدیمی و سمج، بهتر است از شوینده ماشین لباسشویی استفاده شود؛ زیرا شویندههای دستی پاککنندگی کمتری نسبت به شوینده ماشین لباسشویی دارد. بهتر است که شوینده را متناسب با نوع پارچه و میزان کثیفی لباسها انتخاب کنید تا مانع از آسیب دیدن الیاف لباسها شوید. برای مثال، شویندههای دستی گزینه مناسبتری برای شستن لباسهای ابریشمی هستند. از سوی دیگر، شستن لباسهای زیر با ماشین لباسشویی موجب انتشار میکروبها در محفظه بسته دستگاه میشود. پس بهتر است آنها را با استفاده از شوینده دستی بشویید.
شویندههای ماشین لباسشویی به گونهای طراحی شده است که متناسب با قدرت آبکشی و ظرفیت دستگاه باشد. استفاده از سایر شویندهها، این تعادل را برهم میزند و باعث ایجاد لکه سفید روی لباس و کاهش طول عمر دستگاه میشود. برای درک بهتر تفاوت شوینده ماشین لباسشویی با دستی، بهتر است با مزایا و معایب هریک آشنا شوید.
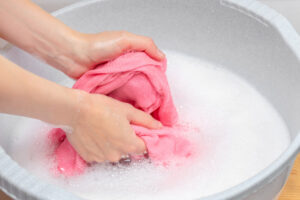
خصوصیت شوینده دستی
- سهولت در شستشوی قالی، فرش و اجسامی که امکان شستشوی آنها با ماشین وجود ندارد
- سهولت در شستشو دستی
- تولید کف زیاد برای از بین بردن لکهها
- احتمال باقی ماندن مواد شوینده بر روی پارچه
- قدرت پاککنندگی ملایم
- احتمال سفیدک زدن لباسهای شسته شده
خصوصیت شوینده ماشین لباسشویی
- حاوی آنزیمهای فعال
- قدرت پاککنندگی، شفافکنندگی و پاککنندگی بالا
- تولید کف کنترل شده
- نیاز به استفاده از نرمکننده برای کاهش چروک لباسها
- احتمال سفیدک زدن لباسها در ماشین لباسشویی
- احتمال ایجاد رسوب در ماشین لباسشویی
نتیجه
در مجموع ، اگر می خواهید پودر شوینده تجاری تولید کنید باید بسیار مطالعه کنید. دانش پایه ای ساخت شوینده ها را کسب کنید، کتاب معتبر بخوانید، این یکی از بهترین روش ها برای ساخت پودر شوینده است.